Top Plastic Testing Techniques: Enhancing Product Performance and Reliability
Top Plastic Testing Techniques: Enhancing Product Performance and Reliability
Blog Article
Top Plastic Testing Techniques: Enhancing Product Performance and Reliability
In the competitive landscape of modern manufacturing, ensuring the performance and reliability of plastic materials is a top priority. From automotive components to consumer products, plastic materials must meet strict industry standards for safety, durability, and efficiency. The only way to guarantee this is through rigorous plastic testing techniques that help manufacturers verify material properties and ensure long-lasting, high-performing products.
This blog will explore the top plastic testing techniques, their significance in improving product performance, and how they contribute to enhancing reliability in various industries.
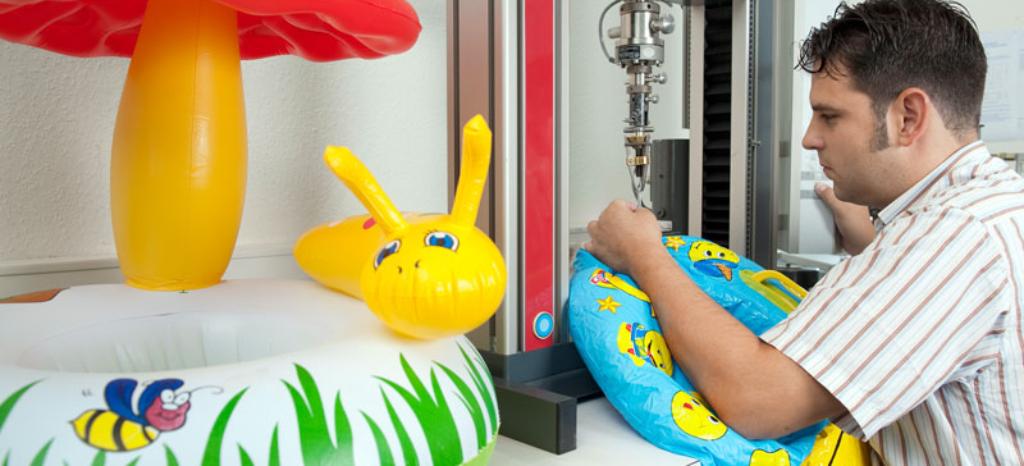
The Role of Plastic Testing in Product Development
Plastic testing is crucial for identifying the characteristics of plastic materials, ensuring they meet specific mechanical, thermal, and chemical requirements. It also aids manufacturers in selecting the right materials for their applications and addressing potential material weaknesses early in the development process.
Ensuring Material Compliance
Plastics used in sectors like aerospace, automotive, and healthcare must comply with stringent industry standards. Testing ensures that these materials adhere to regulations regarding safety, performance, and environmental impact, helping manufacturers avoid product failures and costly recalls.
Improving Product Durability
By rigorously testing plastic materials, manufacturers can increase the durability and lifespan of their products. Whether it’s resistance to environmental factors or mechanical stress, these tests ensure that plastic products retain their performance over time, even under demanding conditions.
Top Plastic Testing Techniques for Enhancing Performance and Reliability
1. Tensile Testing
Tensile testing is one of the most fundamental techniques for evaluating a plastic's mechanical properties. This test measures a material’s ability to withstand pulling forces without breaking, providing insights into the tensile strength, elongation, and modulus of elasticity.
Importance of Tensile Testing
Tensile testing is critical for applications where materials need to endure continuous or sudden stress, such as in packaging, automotive components, and construction materials. By identifying a material's tensile properties, manufacturers can ensure it will not deform or break under pressure, thereby improving product reliability.
2. Flexural Testing
Flexural testing evaluates a plastic material's ability to resist deformation under bending forces. The test determines a material's flexural strength and flexural modulus, providing valuable information about its performance when subjected to bending or compression.
Applications of Flexural Testing
Plastics used in structural applications, such as beams, panels, and support components, must resist bending. Flexural testing helps ensure that materials used in such applications maintain their structural integrity and resist failure under load, enhancing their overall durability.
3. Impact Resistance Testing
Impact resistance testing assesses a plastic material’s ability to absorb energy and withstand sudden impact without fracturing. This test is particularly important for materials that need to resist collision forces, such as automotive parts, sporting equipment, and protective gear.
Significance of Impact Testing
Impact testing ensures that plastic components will not fail when subjected to sudden forces, thus enhancing both performance and safety. Materials with high impact resistance contribute to the longevity and reliability of products used in environments where impacts are common.
4. Thermal Analysis
Thermal analysis involves evaluating how plastic materials behave under varying temperatures. Two of the most commonly used thermal tests include:
- Differential Scanning Calorimetry (DSC): Measures the heat flow into or out of a material as it is heated or cooled, providing insights into melting and crystallization points.
- Thermogravimetric Analysis (TGA): Monitors the weight changes in a material as it is heated, helping determine thermal stability and decomposition characteristics.
Why Thermal Analysis Matters
Thermal analysis is vital for plastics used in applications where they will be exposed to extreme temperatures, such as electronics, automotive engines, and aerospace components. Ensuring that a material can withstand thermal stress without breaking down is crucial for maintaining product reliability.
5. Chemical Resistance Testing
Chemical resistance testing evaluates a plastic material's ability to withstand exposure to various chemicals, including solvents, acids, and oils, without degrading. This is especially important for plastics used in environments where they are likely to come into contact with harsh chemicals.
Applications of Chemical Resistance Testing
Industries like chemical processing, pharmaceuticals, and food packaging rely on plastics that maintain their integrity despite prolonged chemical exposure. Chemical resistance testing ensures that plastic materials do not weaken, dissolve, or leach harmful substances, contributing to product longevity and safety.
6. Flammability Testing
Flammability testing measures how easily a plastic material ignites and how it behaves when exposed to flames. This test is essential for products where fire safety is a concern, such as in electrical housings, automotive interiors, and building materials.
Importance of Flammability Testing
Ensuring that plastic components meet fire safety standards helps protect consumers and prevent accidents. Flammability testing also ensures compliance with regulatory requirements, such as UL (Underwriters Laboratories) certification, enhancing the overall reliability of products.
7. Hardness Testing
Hardness testing measures a plastic's resistance to indentation or scratching, providing insights into its wear resistance and durability. Common hardness tests include the Rockwell and Shore durometer scales.
Applications of Hardness Testing
Hardness testing is crucial for plastics used in high-wear environments, such as in machinery components, consumer electronics, and construction materials. By selecting materials with high hardness values, manufacturers can ensure that their products remain functional and resistant to surface damage over time.
How Plastic Testing Enhances Product Reliability
Identifying Material Weaknesses Early
Plastic testing techniques allow manufacturers to detect material weaknesses early in the design process. By identifying potential failure points before products enter mass production, companies can take corrective action, ensuring their products perform as intended under real-world conditions.
Reducing Product Recalls and Failures
Rigorous testing helps reduce the risk of product failures and costly recalls. By validating that materials meet industry standards for strength, durability, and safety, manufacturers can confidently release products into the market, minimizing the risk of malfunction or defects.
Building Consumer Trust
Consumers expect reliable, high-performing products, and plastic testing is key to meeting these expectations. By ensuring that plastic components are safe, durable, and capable of withstanding harsh conditions, manufacturers can enhance their reputation and build long-term trust with their customers.
Conclusion
Plastic testing plays a critical role in improving product performance and ensuring long-term reliability. From tensile and impact resistance testing to thermal and chemical resistance tests, these methods provide valuable insights into the material properties that are essential for creating high-quality, durable plastic products.
For manufacturers aiming to produce safe, reliable, and long-lasting products, investing in the right plastic testing techniques is essential. Through comprehensive testing, companies can maintain compliance with industry standards, reduce product recalls, and ultimately, enhance consumer satisfaction.
Report this page